SPARK & CO EDM machine supplier provide the EDM process consists of generating an electric arc between a metal part and a graphite electrode. Separating the two is a dielectric, electrically insulating medium. The intensity of the electric field is greater than the resistance of the dielectric, at least at some point, and the current breaks, allowing electrical flow between the electrodes. It is the same effect as the breakdown of an electric capacitor. The spark will heat the surface of the part to a temperature where the metal volatilizes, will remove particles from the part, and will finally be able to reproduce the shapes of the electrode in the part. The typical geometry is three-dimensional formed by various angles.
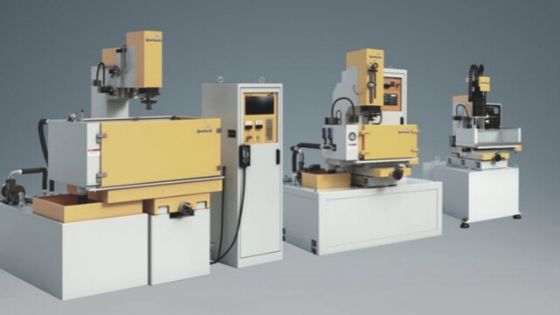
The EDM Machine offers a Variety of Cycles:
The SPARK & CO EDM machine supplier offers Vertical, orbital, vector, directional, helical, conical, rotational, etc. The metal start mechanism is a thermal as well as a mechanical process, caused by the presence of an electrical force on the surface of the electrode, which can mechanically tear off the chip and create a crater. It also suffers erosion.
Basically, it is a series of breaks and restorations of the dielectric liquid between electrodes following a model, producing thousands of sparks. The depth of the crater created depends on the length of the pulse, the longer the finish surface will be rougher. Very short pulse will give a finer finish. During the interval between pulses the dielectric liquid is renewed, the longer the interval, the more liquid is renewed in microseconds, and more metal particles will be thrown out; This removes the danger of a short circuit caused by the particles.
This Wear on the Electrode Geometry has to be Counteracted:
One possibility is to replace it during operation, something easy if we use wire EDM, to carefully push it down. Obviously, when wear is severe the electrode is replaced. If it is graphite, wear is corrected with a millisecond controllable digital generator that reverses polarity while EDM operates. It is an effect similar to the silver coating, which continuously deposits graphite particles backwards, towards the electrode, until achieving zero wear.
The erosion of the piece varies from nanometers to hundreds of microns on rough surfaces. For an accurate finish, ± 0.05 mm, 2 or more electrodes are required, a common practice, when the tool reproduces the desired shape in negative. The tool advances in a single downward direction, the Z axis. When we use a single electrode in a simple way, we have to move it in different directions, and even use its rotation to grind. The wear achieved depends on the polarity, maximum current and applied voltage. The surface roughness (RS) can vary between 48 RS (very rough finish) and 26 RS (almost perfect finish). 0 RS is a smooth finish, almost impossible to achieve.
Ratio Between Length and Diameter
With the shape electrode, no cutting forces are generated, as in machining, turning and drilling processes. Therefore, it is applicable to fragile metals. Very steep holes can be produced on curved surfaces, without slipping problems; as well as high ratio: Ratio between length and diameter. Small diameter and great depth are not possible with a conventional drill.
The tolerances that are obtained are very tight: from ± 0.025 to ± 0.127 mm, and complex configurations are achieved, which were previously impossible. No acid attack required to achieve a rough finish. With the acid, the finish is perfect, reducing costs and machining time, satisfactory in most cases.
Since the geometry of some parts is complex and the necessary cutting work is difficult to position, specific stainless-steel artifacts are used in order to hold the part during the process. We try to make the manufacturing cycle as short as possible; the finish of the piece has the desired roughness and quality and that the precision in dimensions and geometric tolerances are as planned. The pieces to be worked must be arranged so that they require minimal attention during machining. Since there is no direct contact between tool and part, soft metals can be machined without causing any distortion.
Obviously, the protection and safety of the operator is important, as sparks can jump out of the container and the use of high voltage electric current presents an electrocution hazard.
Not everything is an advantage, as a piece finished by chip removal (milling machine, lathe, planner) has more resistance to fatigue than a piece finished by electrical penetration, EDM. The energy consumed is high.
Related Post: