From the outlook, the initial investment in a warehouse management system (WMS) may seem expensive and unnecessary. However, once your warehouse’s processes run on this technology, you can realize various benefits. There are many upsides to having a warehouse management system, ranging from inventory control to labor efficiency, with an overall reduction in cost.
There are various WMS versions in the market, from which you only need to pick one that best fits your operations. It’s important to note that getting the best warehouse management systems provider is crucial too, and you can base your choice on your industry’s standards of operations. Getting the right WMS provider is vital as you may also need post-installation services, such as support in implementation and software updates and upgrades.
With that being said, below are some benefits your business can realize with a fully operational WMS.
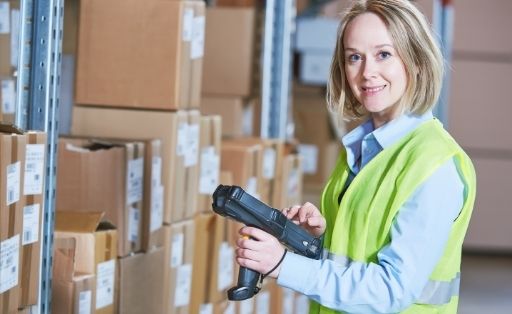
Contents
1. Support Labour Efficiency And Increased Productivity
One of the notable benefits of a warehouse management system is the reduced time your team takes to execute their tasks. You may even manage to run some of these tasks with leaner staffing requirements. With a WMS, you can allocate tasks according to your team’s location and abilities. Doing so reduces travel time; thus, you can achieve more within a shorter period. Coupled with the ability to match tasks as per their capabilities, WMS can help improve the team’s morale and increase their productivity.
Additionally, a warehouse management system can help with day-to-day scheduling through labor forecasting. It can help identify laborious tasks to schedule your team accordingly. Overall, the WMS ensures that you have the right team at the right time and place, providing faster completion of tasks.
Furthermore, WMS’ features like tagging and bar code scanning, the warehouse management system eliminate the need for double-checking. This saves time and also improves pick-up accuracy. Thus, your team can dispense more accurately, which can help boost your customer service rating.
2. Strengthen Supplier And Customer Relationships
A warehouse management system optimizes and streamlines your operations and processes on a broader scale. It provides you with accurate data for staff scheduling, task allocation, accurate invoicing, and efficient dispatch and receiving.
Reduced delivery times mean that your business partners can also efficiently plan their operations from the supplier side. This can also help them reduce their delivery-related costs. Additionally, a WMS increases your reliability and accuracy; thus, your suppliers expect fewer returns and emergency orders. Therefore, they can also manage their inventory at optimum levels.
Customers also benefit from an excellent WMS. Due to the WMS inventory scanning and coding features, your customers can experience accurate and quick order dispatch. This can help improve your reputation within your customer base. The warehouse management system also provides an inventory tracking feature, which notifies the customer of the shipment process and updates your selling platforms with real-time product availability. Such a feature enhances your customer service operations and can help build loyalty.
While the suppliers can rely on your quick receiving process, your customers can expect the correct orders within a short time. In essence, a WMS equips your team for better service delivery on both ends of your supply chain. In addition, it can build confidence in your business, which can help drive your revenue and increase your profit margin.
3. Improve Space Optimisation
With an effective WMS, you can accurately forecast an inventory’s demand requirements. Therefore, you can ensure that you have the correct stock levels. Having the optimum quantity for a particular period means that you can release space for other inventory items.
Additionally, with a WMS, you can practice the just-in-time principle. This principle lets you schedule deliveries just in time for use, dispatch, or pick-up. Thus, you don’t have to hold stock in your warehouse for extended periods. This consequently means you can use the available space for different stock items at other times. For this reason, you can manage to reduce your inventory holding costs.
Recommended: Best Inventory Management Software For Your Business
4. Better Inventory Control
When running a business, you may often run into over or under-stocking, lost stock, or misplaced inventory issues. Such instances can only be compounded if you have a large operation to manage. However, you can minimize these through a WMS through its various features.
For example, WMS integrates features like barcode, radio frequency identification (RFID), and batch numbers. With these features, you can find the location of a particular inventory quickly, whether in transit or within your warehouse. Additionally, batch numbers enable your team to identify which inventory needs to be finished first. This depends on the stock movement principle you use – whether first in, first out (FIFO), first expired, first out (FEFO), highest in, first out (HIFO), or last in, first out (LIFO). In all cases, a WMS batch numbering system can help you efficiently execute the correct stock rotation principle.
Further to inventory location and rotation, a WMS provides you with real-time stock turnover. This means you can manage to keep a tab on the rate of movement of particular stock items. Therefore, it helps you determine re-order levels and quantities. In turn, you can avoid overstocking, leading to dead stock, or under-stocking, which can lead to shortages.
Conclusion
With a fully operational warehouse management system, you can optimize space and improve labor efficiency. At the same time, it also helps smoothens your supply chain processes, thus boosting relationships with your suppliers and customers. In the end, you can recoup more than the initial investment on the WMS solution.