When it comes to maximizing the efficiency of your business, a quality management system is absolutely necessary. Not only will it help you improve the economic, and quality value of your products & services.
But it will also help you command a stronger brand authority, and build an enterprise that consumers trust.
With over 1.1 million certificates issued, over 178 countries, the current rave for SME’s when it comes to Quality Management Systems (QMS) is the ISO 9001 certification.
However, the catch is implementing, and regulating an effective QMS is far easier then it sounds. And it doesn’t sound easy in the first place.
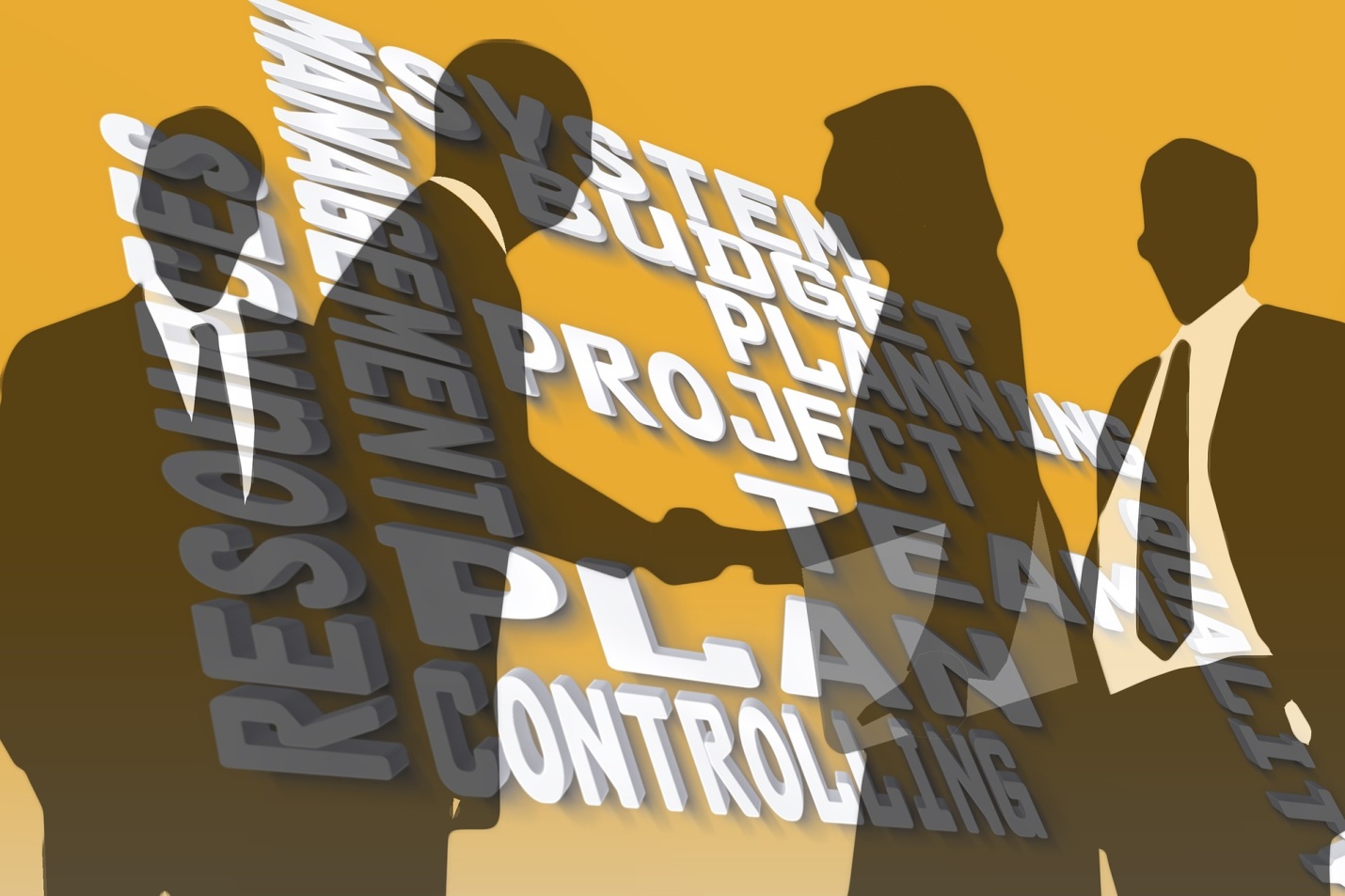
The good news is I plan on addressing three of the key challenges that small, and medium enterprises face when implementing ISO 9001 into their daily operations, and how to overcome these challenges.
What Exactly Is ISO 9001 And How Does It Benefit Your Business?
If you are reading this article, I am going to assume that you know at least the basics of ISO 9001, and QMS integrations. But just in case, I wanted to highlight exactly what ISO 9001 certification is, and why it’s so beneficial to your business.
The entire theory behind the ISO 9001 is constant evaluation, and reevaluation of your QMS. This standard of continuous improvement will not only help ensure you are maximizing your resources on daily operations.
But it will also have a huge impact on the satisfaction of your customers, and your overall brand authority due to continuous improvement of the products/services that you are offering.
The main downfall of getting ISO certification, is the time investment involved for each overhaul.
So What Are The Biggest Challenges SMEs Face With ISO 9001 Certification?
How Much Do You Need To Document
At first glance, knowing what you need to document seems like a breeze. You know, never sweat the small stuff. But once you get started, things can get a tad more complicated.
The first thing to note is there are certain requirements when it comes to documentation as defined in the ISO 9001: 2015.
After you have fulfilled the requirements as listed in the ISO 9001, the rest is actually pretty much up to you. What procedures, and processes are important for conformity through your business?
But from an SME perspective, things can get just a tiny bit worse before they get better. Here are a few small business problems that you may run into:
Do You Actually Use The Procedure You Are Documenting:
There are some procedures and processes that you will only use once in a blue moon. Perhaps a yearly thing. But remember, the entire point of the ISO 9001 is to ensure consistency, and efficiency.
So, regardless of how often you find yourself using any procedures, rather get them documented for quality sakes.
The same applies regardless of how many individuals are responsible for the procedure. It could actually prove beneficial documenting certain one-business procedures.
For example, if the individual who normally covers that role is not available, having it documented could come in rather handy.
What About All Of The Services That I Use Third Party Providers For?
It’s not uncommon for small businesses to outsource work. From being to busy, to not having the required infrastructure to handle the workload – it is a perfectly normal process. But it can make the ISO 9001 a bit complicated considering you need to document every process, right?
The entire point of a QMS is to ensure you have control over every element leading right up to the customers knocking on your door and spending their money on a product. But when it comes to outsourcing, you have very little to no control over the way the third party handles operations.
You need to figure out how to gain at least a measure of control, so you can illustrate it during your ISO 9001 QMS audit.
Don’t Forget To Place A High Focus On Internal Audits
When you are facing the upcoming audit, it can be nerve wracking. A great way to ensure everything is operating smoothly is to regularly conform to internal audits. Evaluate processes, ensure records are flawless, and conduct interviews with those in charge of overviewing specific procedures throughout the operations.
Here is a great article explaining exactly how to handle internal audits for ISO 9001 certification.
Related Post: